La realizzazione di opere nel sotto quota, sottoposte a spinta idraulica, comunemente chiamate ambienti interrati, richiede un’attenta analisi preliminare del contesto geologico in cui si andrà ad operare, oltre che un particolare approccio alle molteplici problematiche progettuali, parecchio diverse dalla comune progettazione delle opere fuori terra.
Per quanto riguarda la fase provvisionale di cantiere, andranno progettate quelle opere che consentano di realizzare lo scavo senza turbare i terreni adiacenti, soprattutto nel caso frequente in ambito urbano di presenza di altri edifici in fregio al confine. Trattasi normalmente di paratie, diaframmi o micropali, generalmente tirantate e di un eventuale tampone di fondo, nel caso di presenza di acqua di falda con un elevato battente rispetto alla quota di fondo scavo, oltre alle opere di “prosciugamento” necessarie a deprimere la quota della falda, al fine di rendere asciutto il fondo scavo.
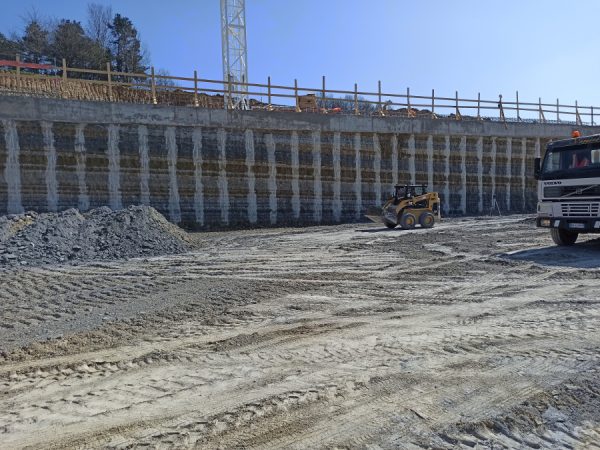
In fase di cantiere, se vi è necessità di deprimere la falda, risulta importante porre attenzione al progetto di aggottamento e coinvolgere un geotecnico in modo tale che non si verifichino dannosi assestamenti del terreno di fondazione degli edifici presenti a confine. Successivamente si potrà procedere alla progettazione delle strutture interne e alla loro impermeabilizzazione fin sotto il livello della falda di progetto in modo da contrastare le spinte idrostatiche.
Queste particolari attenzioni si collegano alla durabilità e alla funzionalità dell’opera nell’intera sua “vita” intesa come periodo che segue l’edificazione.
Il concetto di durabilità si riferisce alla capacità di un’opera di sopportare gli attacchi di agenti aggressivi di diversa natura e l’invecchiamento a causa del passare del tempo, mantenendo inalterate le caratteristiche funzionali e fisiche.
Nel momento in cui vi sono delle problematiche da affrontare, le strutture nel sotto quota risultano spesso di difficile riparazione una volta costruite. Partendo dalle analisi geologiche dei terreni e dalla situazione dell’acqua di falda, non si può quindi prescindere da un’accurata progettazione.
Nella maggior parte dei casi, l’inadeguatezza ed il precoce ammaloramento di ambienti interrati sono imputabili a due errori fondamentali.
Il primo fa riferimento alla mancata considerazione dell’acqua come elemento che può presentarsi sotto varie forme:
- acqua ascendente dal suolo per capillarità o per spinta in presenza di una falda freatica;
- acqua meteorica di dilavamento;
- acqua prodotta e contenuta sotto forma di vapore.
Il secondo è legato alla fase di progettazione. Molto spesso il manto impermeabile scelto non è adatto a resistere a contrasto con carichi e dinamiche che l’acqua può esercitare riversandosi poi contro l’opera strutturale.
Errori aggravati dalla mancanza di un quadro normativo di riferimento che, senza un adeguato percorso formativo, delega la ricerca di soluzioni spesso empiriche alla coscienziosità dei progettisti. Tutto ciò causa inevitabili ripercussioni sulla qualità delle opere realizzate e sul mantenimento dei valori minimi prestazionali di sicurezza, fruibilità e caratteristiche estetiche delle strutture in essere.
La qualità e la durabilità delle strutture interrate sono direttamente proporzionali all’accuratezza della progettazione, intesa come diagnosi, realizzazione e prevenzione, dei sistemi protettivi. Vanno quindi studiate e pianificate in modo dettagliato la tipologia e la metodologia dell’impermeabilizzazione da adattare al contesto e alla specificità delle opere da realizzare, proteggere e preservare nel tempo.
L’impermeabilizzazione interrata e controterra deve compiere simultaneamente più funzionalità:
- drenaggio: permettere all’acqua di defluire ed essere così smaltita;
- tenuta all’acqua:impedire che l’acqua penetri e intacchi le strutture interrate e controterra;
- protezione: resistere agli agenti chimici, ai batteri e alle muffe presenti nella terra, nonché impedire all’apparato radicale della vegetazione circostante l’edificio di perforare l’impermeabilizzazione.
E deve essere:
- resistente a qualsiasi sostanza aggressiva di natura acida e basica;
- impenetrabile dall’acqua;
- resistente alle sollecitazioni meccaniche ed elastiche; in particolar modo deve essere resistente al punzonamento (non perforabile) e alla lacerazione;
- resistente agli agenti atmosferici.
I sistemi di impermeabilizzazione controterra si possono distinguere in:
- Membrane bituminose
- Coatings rigidi o flessibili
- Membrane bentonitiche
- Membrane sintetiche
- Membrane sintetiche autosigillanti
Membrane bituminose
Oggi alcune membrane vengono realizzate unendo i due polimeri maggiormente utilizzati, l’APP (polipropilene atattico) e l’SBS (stirene-butadiene-stirene).
Il polipropilene atattico rientra nella categoria delle poliolefine e si ottiene per polimerizzazione del propilene. Le membrane così conseguite vengono chiamate plastomeriche, in quanto il comportamento può essere assimilabile a quello di un materiale plastico.
Sono membrane confezionate in rotoli e preformate da componenti a base bituminosa con additivi polimerici che le conferiscono il comportamento elastico del rivestimento, ovvero quella capacità di ritornare, dopo uno sforzo, alla forma originaria e si possono suddividere in:
- plastomerica: superato un certo limite di carico la deformazione è irreversibile;
- elastomerica:la deformazione sotto carico è completamente reversibile, ma richiede una posa altamente specializzata;
- elastoplastomerica: ha un comportamento misto tra le precedenti soluzioni.
Coatings rigidi o flessibili
Per meglio curare tutti i dettagli di una costruzione bisogna affidarsi ad una serie di prodotti progettati per unirsi tra loro.
I prodotti impermeabilizzanti di questa categoria comprendono varie tipologie di formulati, partendo dalle materie prime che le compongono si possono così dividere:
- prodotti a base di resine termoindurenti: epossidiche, poliuretaniche, poliestere, con varie combinazioni di cariche ed additivi (es. epossicemento);
- prodotti a base di resine termoplastiche: acriliche, viniliche, poliuretaniche, a volte denominate commercialmente “guaine liquide”;
- prodotti a base bituminosa: formulati come prodotti liquidi o in pasta, combinati con altre resine o additivi;
- prodotti a base cementizia e/o minerale: monocomponenti, bicomponenti, pronti all’uso, oppure partendo da miscele di cemento e/o minerali ed inerti confezionati sul posto con l’ausilio di additivi specifici.
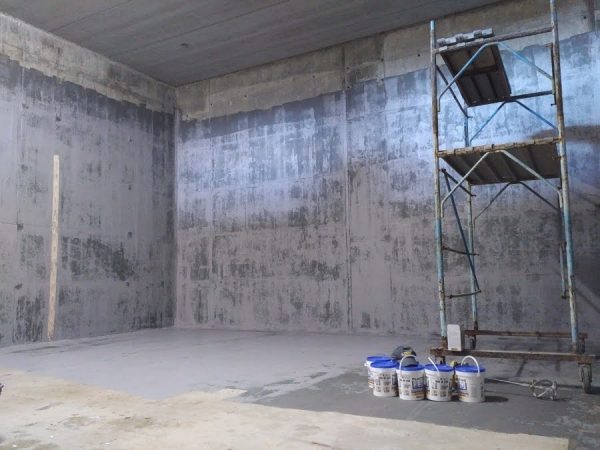
Esempio di applicazione coating flessibile dall’interno
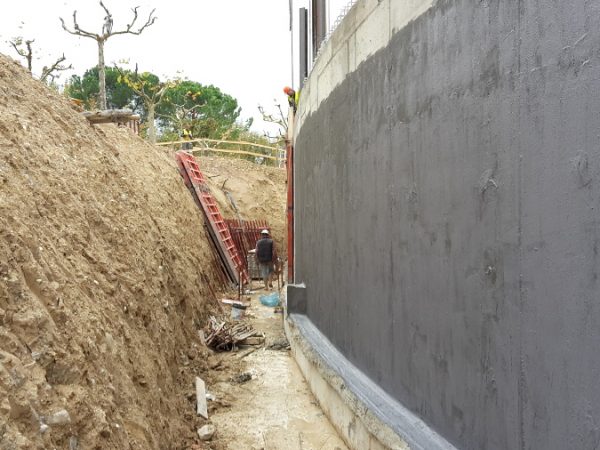
Esempio di applicazione coating flessibile dall’esterno
Membrane bentonitiche
Le membrane betonitiche rappresentano una modalità impermeabilizzante differente che, una volta entrata a contatto con l’acqua, crea una protezione permanente.
La bentonite è una argilla di origine vulcanica datata circa 50 – 130 milioni di anni fa ed ha l’importante proprietà di aumentare di volume se viene a contatto con l’acqua/umidità. Normalmente viene utilizzata la membrana di sodio, di qualità maggiore rispetto a quella di calcio, che è composta principalmente dal minerale montmorillonite costituito a sua volta da silicio ed alluminio e sodio.
Ad oggi viene prodotta sotto forma di pannelli di cordoli, di profilati o di geotessuti, questi ultimi anche di grandi dimensioni.
Le principali famiglie di prodotti utilizzati sono:
- bentonite allo stato naturale;
- bentonite trattata mediante polimeri; è resistente agli inquinanti chimici;
- bentonite pre-idratata; resistente agli inquinanti chimici e a contatto con acqua salata.
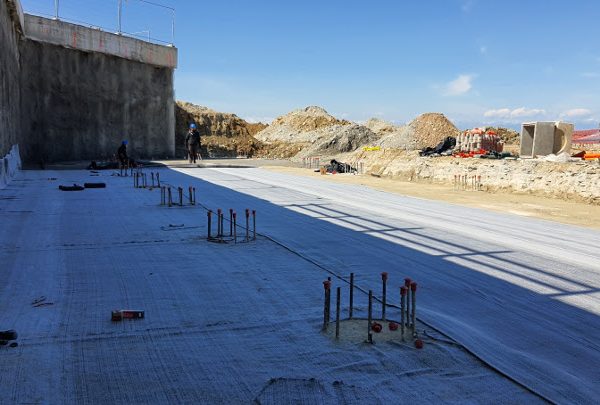
Esempio di applicazione membrana bentonitica
Membrane sintetiche
Le membrane sintetiche sono prodotti di pura sintesi, a differenza di quelle bituminose, che vengono utilizzate per la loro capacità di deformazione dimensionale e per la resistenza ad elementi degradanti che disgregano gli altri sistemi, ad esempio in discariche o serbatoi di raccolta dei reflui o, ancora, raccolte di olii.
Tra i vari punti di forza vi è la possibilità di avere teli di grandi dimensioni (l’EPDM) o grande resistenza chimica (l’HDPE viene usato nelle discariche); comunque la deformabilità di tipo elastico li vede maggiormente impiegati dove le tensioni normali sono maggiori o dove le grandi dimensioni li rendono economici.
Sono diverse tipologie di membrane derivanti da processi industriali che permetto tramite differenti tipi di polimeri, di creare prodotti impermeabili, resistenti e duraturi nel tempo.
Le membrane sintetiche più utilizzate per l’impermeabilizzazione delle fondazioni sono di diverse tipologie:
- in cloruro di polivinile (PVC): materiale rigido che se miscelato con composti inorganici e prodotti plastificanti, può diventare flessibile e modellabile;
- a base di poliolefine (TPO o FPA): famiglia di materie plastiche che si distingue per l’elevata resistenza agli agenti chimici e per l’elevata versatilità;
- polietilene ad alta densità (HDPE) materiale con resistenza a trazione maggiore, più duro e opaco, ha buone caratteristiche di resistenza al fuoco;
- elastomero (EPDM): famiglia di gomme sintetiche, resistente all’ aggressione di fluidi idraulici, acqua calda/fredda e agli alcali.
Membrane sintetiche autosigillanti
Esiste una nuova generazione di membrane autosigillanti che sono il risultato dell’evoluzione delle membrane sintetiche di cui si è precedentemente parlato. Queste membrane hanno la peculiarità di integrare specifici polimeri idroespansivi che permettono, in condizioni di esercizio, l’autosigillatura qualora si verificassero delle forature nel manto impermeabile.
Tali rivestimenti sono composti da un manto continuo polimerico multistrato coestruso, con funzionalità differenziate: un primo strato esterno in EPDM totalmente impermeabile, uno strato centrale in polimeri idroespansivi dall’alta capacità sigillante e un terzo strato idroespansivo che evita così la migrazione laterale dell’acqua essendo abbinato ad un tessuto non tessuto che ne consente l’adesione meccanica con la struttura il calcestruzzo.
In questi ultimi anni le aziende produttrici hanno migliorato la qualità e le prestazioni dei prodotti, ma questo non basta. Il successo di un sistema di impermeabilizzazione, infatti, oltre che dalla coerenza del sistema stesso rispetto al modello d’uso e al contesto tecnico e ambientale, dipende in larga parte dalla sua corretta progettazione e realizzazione in corso d’opera e la posa dei sistemi scelti deve essere demandata a personale specializzato, formato e aggiornato.
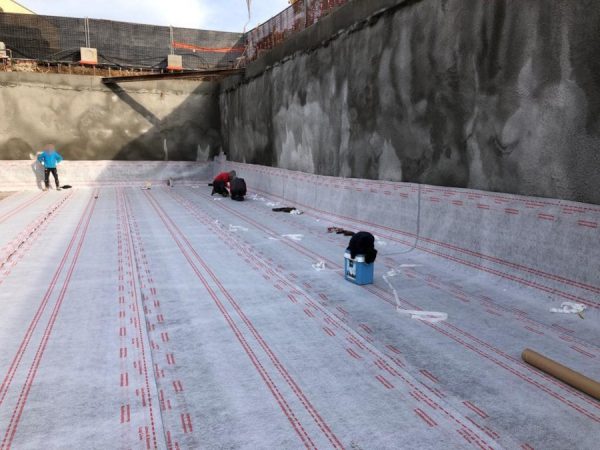
Esempio di applicazione membrana sintetica autosigillante in platea
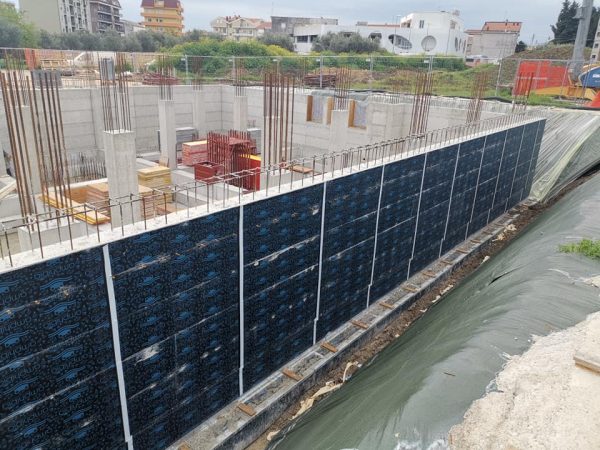
Esempio di applicazione membrana sintetica autosigillante verticale sui muri